Precast Concrete
Industrualization in the construction of buildings is a natural development as has also happened to other industries. It is slower than the others because of the greater obstacles encountered in the building industry, which is not just a fashionable trend, but also related to the demanding value statement: Changes in the mental attitude and new thinking of some building experts.
During this time people feel attached to the house that should be respected individually, then of course people will feel something else when suddenly accommodation shelter:
- Provided in the form of non-building blocks or flats as usual.
- Buildings are not specifically designed as individual user requests.
- Buildings are established in the form of finished products without any further intervention from the wearer.
- Buildings are designed with a similar appearance or even the same.
- Direct building tools so if you want to design and build individually.
- With a very limited choice.
The building industry should also make progress on the use of cranes and other machines but in a broader way. The lag in the building industry is developed in an industrialized way that is terotomastized throughout the process since preparation and molding, casting, concreting, prestressing, storage, transportation, erection ), lifting (lifting) and handling (handling).
Prefabrication is the industrialization of construction methods in which the components are mass-produced assembled in buildings with the help of cranes and other lifting and handling devices.
Prefabricated Structural Components are made from concrete through precast units / precast numbers or precast elements depending on the alternative use, well controlled printing is given time for hardening and achieves certain desired strengths before being lifted and brought to the construction site indeed for development. The construction method created using prefabricated components is collectively referred to as 'prefabricated contruction' (prefabricated construction). Prefabricated Construction may be the main building activity sector: industrial architecture (Industrial architecture), General Engineering (Engineering structures in general) and Civil Engineering.
Precast Structural Components, an alternative made to buildings on a particular site. This trend leads to component manufacturers.
Prefabrication is the industrialization of construction methods in which the components are mass-produced assembled in buildings with the help of cranes and other lifting and handling devices.
Prefabricated Structural Components are made from concrete through precast units / precast numbers or precast elements depending on the alternative use, well controlled printing is given time for hardening and achieves certain desired strengths before being lifted and brought to the construction site indeed for development. The construction method created using prefabricated components is collectively referred to as 'prefabricated contruction' (prefabricated construction). Prefabricated Construction may be the main building activity sector: industrial architecture (Industrial architecture), General Engineering (Engineering structures in general) and Civil Engineering.
Precast Structural Components, an alternative made to buildings on a particular site. This trend leads to component manufacturers.
Problem Material
Ideal requirements that must be met in building construction techniques with prefabricated construction systems:
Ideal requirements that must be met in building construction techniques with prefabricated construction systems:
- The ability to manufacture through mechanical methods (congenital loads and closed components).
- Possible connections and structural connections are feasible and allow to be made in the simplest way.
- Simultaneously the possibility for the implementation of its function due to the innate load and space limitation of motion.
The most important thing is that the material must have the following qualifications:
- Isolate heat, water resistance and anti-decay.
- Anti-flame and can be printed volumetrically.
- Can be nailed and sawed to allow for change.
- Not much need maintenance (maintenance).
- Has high strength.
Advantages and Problems of Prefabricated Construction
Some of the advantages of prefabricated construction in the building industry are:
- Faster construction time, since structural work on site, foundation construction and establishment of prefabricated components.
- The amount of material required is not reduced
- The production of large-scale precast units makes it more practical to use machinery and hence the need for an excessive number of workers can be overcome
- Reduced human labor needs and demands more skill
- The resulting quality is better as a result of factory processes that are always under close and steady supervision, the use of machines and a tidy working environment
- Construction work can be carried out without depending on weather conditions
Problems in prefabricated construction are:
- Transport component from factory to project
- Difficulties in handling in the field, especially in erection (establishment), lifting (lifting) and connecting (connection at the time of finalization of construction)
- Such implementation means there are additional costs and technical problems.
History of Precast System Development
Concrete is a widely used construction material in Indonesia, when compared to other materials such as wood and steel. This is understandable, because the ingredients of formation easily available in Indonesia, quite durable, easily formed and the price is relatively affordable. There are several aspects that can be of concern in conventional concrete systems, such as long and poor clean run times, difficult quality controls and base materials of increasingly expensive and rare molds of wood and plywood.
The precast concrete system is a construction method that can answer the needs of this new millennium era. Basically, this system performs casting components in a special place on the ground surface (fabrication), then taken to the location (transportation) to be structured into a whole structure (erection). The advantages of this system, including assured quality, fast and mass production, rapid development, environmentally friendly and tidy with good product quality. A qualitative comparison between wood, steel and conventional and precast concrete structures can be seen in the table below
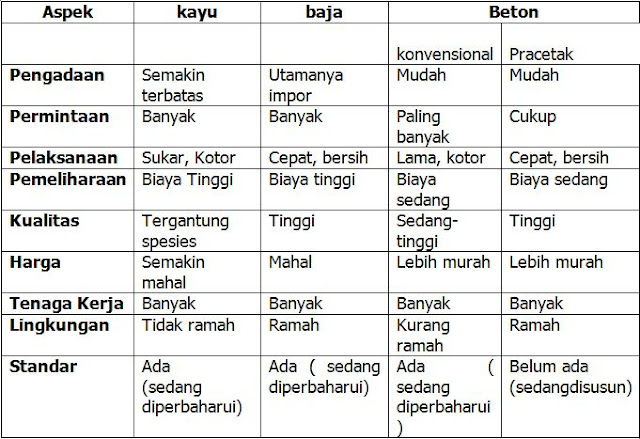
Preprint systems have been widely applied in Indonesia, both of which are developed domestically or imported from abroad. Precraft systems in the form of components, such as piles, bridge beams, beach plate columns. The fundamental issues in the development of precast systems in Indonesia today are:
- The system is relatively new
- Less socialized type, product and the ability of precast system that already exist
- And the constraints of connection between components for the precast system to the seismic load always become a reality
- The absence of official guidance on the procedures of analysis, planning and the level of specific constraints for precast systems that can be used as guidelines for the perpetrators of construction.
Development of Precast System In The World
Modern precast system developed early in the European Country. The precast structures were first used as precrete concrete blocks for the Casino in Biarritz, built by Coignet contractor Paris 1891. The reinforced concrete foundation was introduced by a German company, Wayss & Freytag in Hamburg and began to be used in 1906. In 1912 several high rise buildings precast system in the form of components, such as walls, columns and floors introduced by John.E.Conzelmann.
The structure of prefabricated reinforced concrete components was also introduced in Germany by Philip Holzmann AG, Dyckerhoff & Widmann G Wayss & Freytag KG, Prteussag, Loser etc. Earthquake resistant precast system pioneered its development in New Zealand. America and Japan, known as a developed country in the world, did new intensive research on earthquake resistant precast system in 1991. By creating a joint research program called PRESS (Precast seismic Structure System).
The structure of prefabricated reinforced concrete components was also introduced in Germany by Philip Holzmann AG, Dyckerhoff & Widmann G Wayss & Freytag KG, Prteussag, Loser etc. Earthquake resistant precast system pioneered its development in New Zealand. America and Japan, known as a developed country in the world, did new intensive research on earthquake resistant precast system in 1991. By creating a joint research program called PRESS (Precast seismic Structure System).
Development of Prefabricated System In Indonesia
Indonesia has been familiar with precast system components such as piles, bridge beams, columns and floor plates since the 1970s. The precast system is growing with marked emergence of innovations such as Column Slab System (1996), L-Shape Wall System (1996), All Load Bearing Wall System (1997), Beam Column Slab System (1998), Jasubakim System (1999) Bresphaka (1999) and the T-Cap (2000) system.
Common Problems On Precast Concrete System Development
There are three major problems in the development of precast systems:
- Connection constraints between components
- The absence of a specific planning guideline for precast structural systems
- Cooperation with planners in other related fields, especially with architectural and mechanical / electrical / plumbing parties.
Concrete Precision System
In the construction of structures with concrete materials known 3 (three) common development methods, namely conventional systems, formwork systems and precast systems.
Conversion systems are methods that use traditional wood and plywood materials as formwork and scaffolding, as well as casting on-site concrete. The formwork system has stepped forward from a conventional system with the use of formwork systems and metal scaffolding. Formwork system that has been entered in Indonesia, including Outinord and Mivan systems. Outinord system uses steel material while Mivan system uses aluminum material.
In precast system, all building components can be fabricated and then installed in the field. The process of making components can be done with good quality dick.
Conversion systems are methods that use traditional wood and plywood materials as formwork and scaffolding, as well as casting on-site concrete. The formwork system has stepped forward from a conventional system with the use of formwork systems and metal scaffolding. Formwork system that has been entered in Indonesia, including Outinord and Mivan systems. Outinord system uses steel material while Mivan system uses aluminum material.
In precast system, all building components can be fabricated and then installed in the field. The process of making components can be done with good quality dick.
Method of Precast Concrete Implementation
Precast concrete is concrete molded in several locations (both in print in the environment and in factories). According to SKSNI T-15-1991-03 precast concrete is a concrete component that is casted in a place that is not an end position in a structure. Concrete strength used is about 4000 to 6000 psi and with higher strength. Concrete cast in place require more formwork and minimal in maximal reuse 10 times, while for precast concrete formwork of wood or fiber glass can be used to 50 times with little improvement.
Precast concrete is concrete molded in several locations (both in print in the environment and in factories). According to SKSNI T-15-1991-03 precast concrete is a concrete component that is casted in a place that is not an end position in a structure. Concrete strength used is about 4000 to 6000 psi and with higher strength. Concrete cast in place require more formwork and minimal in maximal reuse 10 times, while for precast concrete formwork of wood or fiber glass can be used to 50 times with little improvement.
Iron Precast Cloth Beam
Precast Concrete Casting
Preheated Precast Concrete
Precast Concrete Assembly
Transportation of the precast element will be installed must at least consider the following:
- How long does it take to reach the site.
- Schedule of preprinted elements as scheduled.
- Alternative roads that pass if there is one way happened obstacles.
- Capacity of project location in receiving delivery of precast elements.
- The ability of cranes in lifting the precast elements.
In the installation of the precast element to the location of its last position, several things to note are:
- Site Plan
- Equipment
- Installation Cycle
- Labor
Site Plan
Site Plan that there will be obtained things as follows:
Site Plan that there will be obtained things as follows:
- Can place crane position at project location so that it can be functioned as maximal in precast elements to its last position.
- Places where precast stacking can be arranged to facilitate the arrangement.
Equipment
In the use of precast elements, the following considerations are:
In the use of precast elements, the following considerations are:
- Some cranes are required in a project to be used as much as possible.
- What is the radius of crane rotation.
- Auxiliary equipment as well as the number of needs to support the installation cycle of precast elements such as trucks, and so forth.
Installation Cycle
Broadly speaking the installation cycle of precast elements can be described as follows:
Broadly speaking the installation cycle of precast elements can be described as follows:
- Painting of poer elements
- Installation of beam elements
- Installation of plate elements
- Casting over topping
Some types of precast elements are :
- POER PRECAST
- BALOK PRECAST
- HALF SLAB PRECAST
- PLANK FENDER PRECAST
- DOLPHIN
- KANSTEEN PRECAST
0 comments:
Post a Comment